Engineering
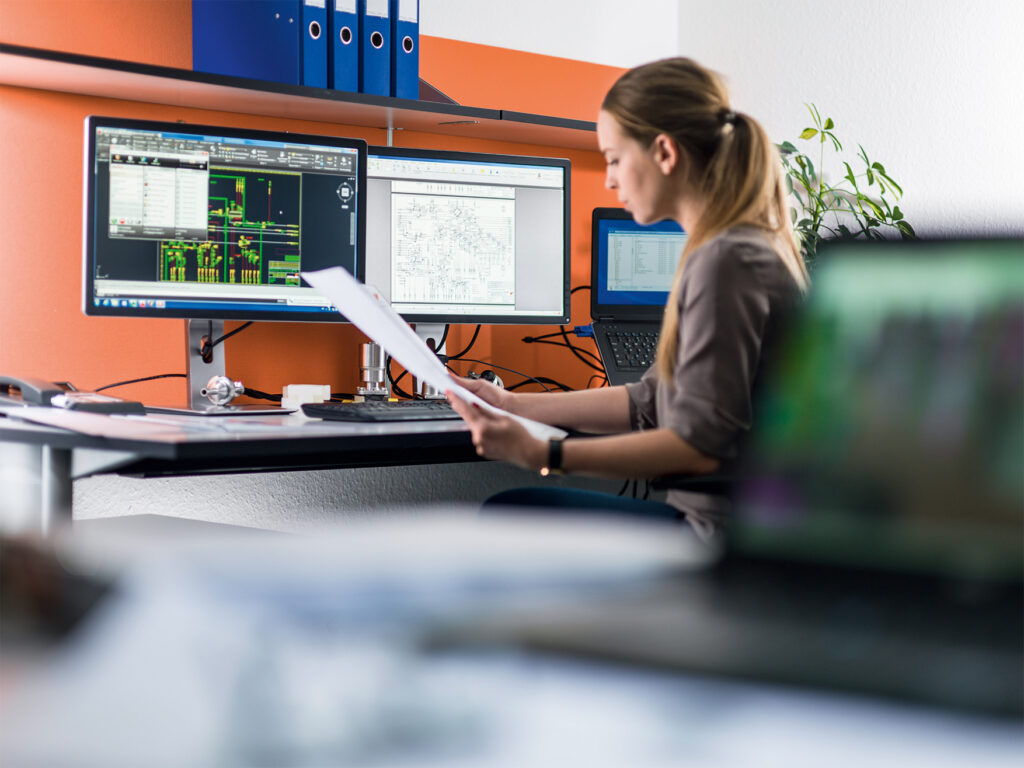
From the initial feasibility study to detailed 3D planning, VOGELBUSCH BIOPHARMA offers all the engineering services required for the realization of biopharmaceutical production facilities. These services are based on the needs and standards of our customers, enabling us to offer tailor-made solutions or develop them in cooperation with our customers. No matter whether it’s about new plants, new plant components or converting existing facilities: our highly skilled team of process engineers, technicians and 2D/3D planners can always lend assistance and support in each and every project stage.
Conceptual stage | consultation
We advise and assist you right from the start, no matter whether it’s about a process scale-up, process optimization or the preparation of basic documents for investment decisions. Based on GMP and ISPE guidelines, we develop concepts for the layout of your facilities, their personnel and material flow, their cleaning as well as for the process itself. After assessing equipment and facility dimensions, we compile the corresponding cost estimates and implementation schedules.
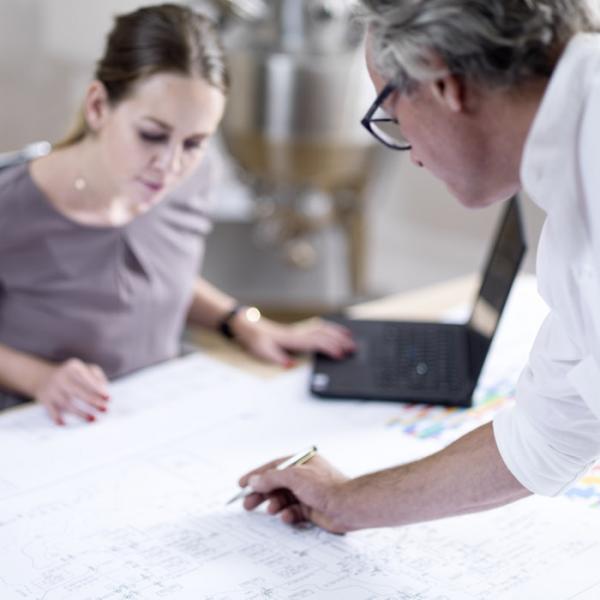
We also advise in defining and determining equipment standards, for a well thought-out concept facilitates all subsequent process steps significantly.
After assessing equipment and facility dimensions, we compile the corresponding cost estimates and implementation schedules. We also advise in defining and determining equipment standards, for a well thought-out concept facilitates all subsequent process steps significantly.
Basic/detail engineering
From block flow diagrams (BFD) and process flow charts (PFC) to piping and instrumentation
diagrams (P&ID): our know-how and flexible engineering tools allow us to prepare the basic documents for every type of plant according to process requirements and the customer’s needs.
Concurrently, we generate important information such as load plans, room thermal loads, electrical connected loads as well as data on supply and disposal system demand. These details will then be provided to all involved trades for further planning.
Process analyses and process modeling (time & motion studies) allow us to plot timelines and identify potential points of failure at an early stage. Mass and energy balances are used to determine equipment size and specifications that are necessary for the procurement of suitable equipment. Our team will also take care of all subsequent stages of execution.
2D layout planning is used to design piping routes and prepare a comprehensive 3D model of your facility which will then serve as a basis for the actual installation of pipe systems.
Concurrently, we will prepare the appropriate automation concept.
All planning steps are documented according to the ISO 9001:2015 certified quality management system of VOGELBUSCH BIOPHARMA in order to ensure seamless traceability and transparency.
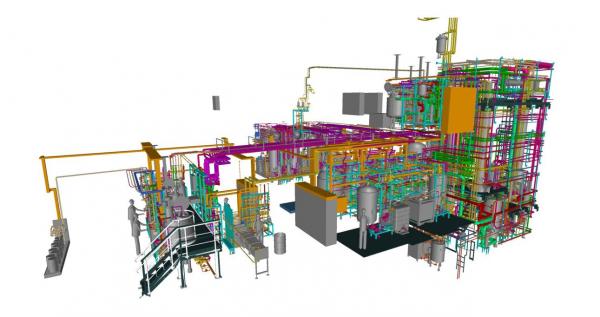
Engineering tools
Software tools are crucial for efficient engineering – VOGELBUSCH BIOPHARMA utilizes various CAD (Computer Aided Design) and CAE (Computer Aided Engineering) methods:
To our staff, it makes no difference whether a system has been specified by the customer or is supplied by VOGELBUSCH BIOPHARMA in its entirety using tried-and-tested designs.
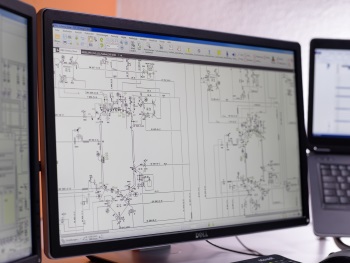
A proprietary database system features intelligent data handling in order to provide a maximum of flexibility, customer focus and efficiency, while relying on standard software.
Specialized systems using dedicated pharmaceutical databases such as Comos, AutoCAD, E3D, ePLAN and AVEVA (from the process flow chart to the complete 3D model and finally isometry).
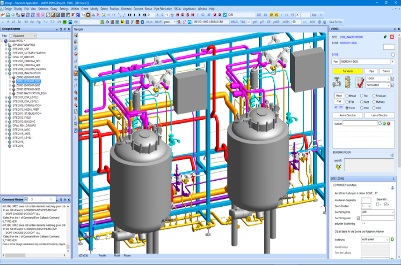
Budgeting
The first budget plans in the form of a detailed cost estimate are available as soon as the basic engineering phase has been completed. Throughout the more detailed engineering and implementation process, monthly expenses are monitored and compared with the relevant final costs, based on estimated costs and project cost forecasts. Any modification in the scope of services is reviewed and assessed based on its cost before being included in the budget plans. This guarantees, that our customers are able to stay on top of overall facility construction costs at all times.
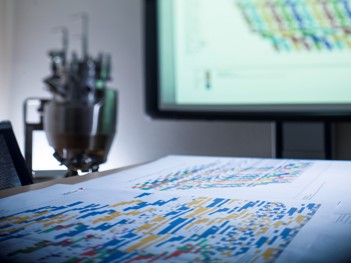
Concept development & automation
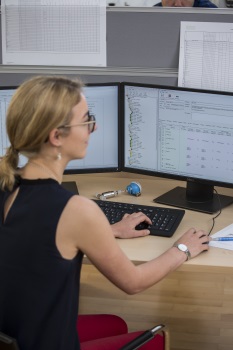
Which degree of automation will we need for our facility? Which hardware manufacturer or systems supplier is most suited for this plant? What are the issues to consider with regard to interfaces with other systems? How much time and effort is needed for specifications, programming, testing and commissioning? How can the new systems be integrated into existing ones?
These are just a few examples for questions that will arise when developing a concept for the automation of pharmaceutical process plants and facilities. We will present different solutions and discuss their pros and cons with our customers in order to design process facilities in line with the needs of their future operators.